
Technology
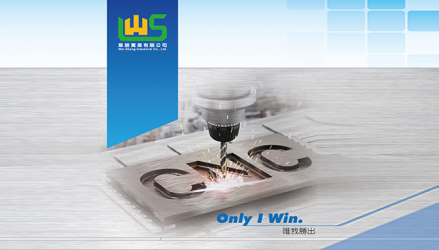
CNC Technology Driven by Artificial Intelligence
Application of Artificial Intelligence (AI) in CNC Numerical Control Technology, The integration of Artificial Intelligence (AI) into CNC numerical control technology has brought significant innovation and enhancement to modern manufacturing. As AI technology continues to mature, CNC systems are transitioning from traditional numerical control to intelligent numerical control. This transformation is primarily reflected in the following aspects:
• Intelligent Optimization of Machining Parameters
AI assists CNC systems in automatically optimizing machining parameters, such as feed rate, cutting speed, and tool paths. By analyzing a vast amount of historical data, AI can identify the best machining strategies, thereby improving machining efficiency, reducing processing time, and minimizing material waste. Additionally, AI can dynamically adjust machining parameters according to different workpiece materials and shapes to ensure consistent machining quality.
• Automatic Fault Diagnosis and Predictive Maintenance
AI-driven CNC systems can monitor the operational status of machines in real-time by detecting anomalies through sensor data. For instance, AI can analyze data on machine vibrations, temperature, and sound to predict potential failures and issue maintenance warnings in advance. This predictive maintenance effectively reduces machine downtime, lowers maintenance costs, and extends equipment lifespan.
• Intelligent Monitoring of the Machining Process
AI technology enables CNC systems to monitor the machining process in real-time and automatically identify abnormalities (such as tool wear or poor workpiece surface quality). When the system detects an anomaly, AI can make immediate adjustments, such as changing tools or modifying machining paths, to ensure the quality of the machining results.
• Learning and Adaptive Capabilities
AI endows CNC systems with learning capabilities, meaning that the system can learn from past machining tasks and continually improve its machining strategies. This adaptive learning ability allows CNC systems to become increasingly intelligent over time, capable of handling more complex and variable machining tasks.
• Human-Machine Collaboration
AI also enhances the collaboration between CNC systems and operators. Intelligent CNC systems can understand operators' instructions through natural language processing and provide optimal operation suggestions. This not only simplifies the operation process but also reduces the skill requirements for operators, enabling even novices to easily operate complex CNC machines.
• Integration of Automated Design and Manufacturing
AI technology helps seamlessly integrate the design and manufacturing processes. For example, AI can automatically analyze design drawings, generate optimal machining plans, and directly output them to CNC machines for processing. This integration of design and manufacturing significantly shortens product development cycles and improves production efficiency.
• Quality Inspection and Feedback
AI can also be applied to post-machining quality inspection. CNC systems can use computer vision technology to automatically inspect the dimensional accuracy and surface quality of workpieces, and feedback the inspection results to the machining system for further optimization of future processes.
The introduction of Artificial Intelligence has made CNC numerical control technology more intelligent, efficient, and reliable. This technological leap not only enhances the competitiveness of the manufacturing industry but also drives the development of Industry 4.0 and smart factories. As AI technology continues to advance, the application scope of CNC numerical control technology will expand, profoundly impacting the future development of the manufacturing industry.