
Technology
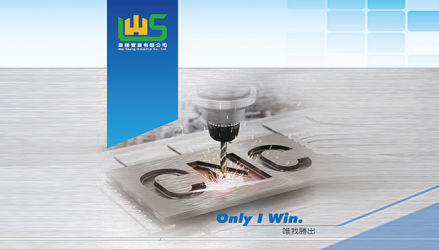
Differences Between CNC Milling and Traditional Milling
CNC milling and traditional milling differ significantly in terms of technology, operation methods, precision, and production efficiency. Here are the main distinctions between these two types of milling:
1. Control Method
• CNC Milling: Controlled by a computer numerical control (CNC) system. Operators write machining programs using software, which precisely controls the machine's movements, including tool paths, feed rates, and cutting depths.
• Traditional Milling: Typically controlled manually by the operator or through simple mechanical devices. Requires the operator to have significant experience to ensure precise control.
2. Machining Precision
• CNC Milling: Offers extremely high precision, often achieving micron-level accuracy. Due to automation and computer control, CNC milling maintains high consistency in machining quality, suitable for mass production.
• Traditional Milling: Generally has lower precision, relying on the operator's skill and experience. It is challenging to maintain consistency, especially when producing complex or high-precision parts.
3. Operation Efficiency
• CNC Milling: Capable of continuous automatic operation, ideal for high-volume and efficient production. CNC mills can process multiple parts without interruption and can use automatic tool changers for various operations.
• Traditional Milling: Requires manual adjustments and operations, needing re-setup for each part, resulting in lower efficiency. It is suitable for small batch or single-piece production.
4. Complex Shape Machining
• CNC Milling: Able to machine very complex three-dimensional shapes. Multi-axis CNC mills, such as five-axis or six-axis, can perform machining on multiple axes simultaneously, making them suitable for complex parts like turbine blades and molds.
• Traditional Milling: Limited in its ability to machine complex shapes, typically handling simple flat and two-dimensional shapes. Machining complex geometries requires multiple setups and tool changes.
5. Operator Skill Requirements
• CNC Milling: Requires operators to have programming skills and knowledge of machine settings, and to be familiar with CAD/CAM software. Manual skill requirements for operating the machine are relatively low.
• Traditional Milling: Requires higher manual operation skills, with operators needing extensive experience to perform precise machining.
6. Production Flexibility
• CNC Milling: Highly flexible, as changing the design and production process can be done quickly by modifying the program. Suitable for diverse and small-batch production.
• Traditional Milling: Less flexible, requiring re-setup for each change in part design, increasing setup time and complexity.
7. Cost
• CNC Milling: Higher initial equipment investment but lower long-term operating costs due to efficiency and automation, making it suitable for large-scale production.
• Traditional Milling: Lower equipment cost but higher operating costs, particularly in mass production due to significant labor costs.
These differences highlight the advantages of CNC milling over traditional milling in modern manufacturing, especially for high-precision, high-volume, and complex shape applications.