
Technology
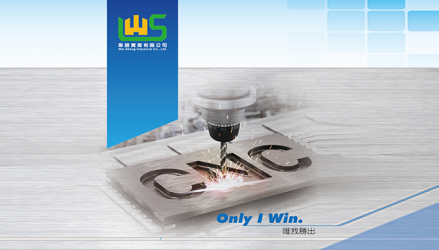
CNC Five-Axis Gantry Machining Centers and Precision Technology
CNC five-axis gantry machining centers are cutting-edge, high-precision CNC machines designed to meet the demands of intricate machining. These machines can move across multiple axes simultaneously, allowing them to process highly complex components with stringent precision and surface quality requirements, such as turbine blades in the aerospace industry, large molds, and various complex curved structures. Renowned for their exceptional multi-axis coordination and high stability, CNC five-axis gantry machining centers are core equipment in industries such as aerospace, automotive manufacturing, energy equipment, and high-end mold production. They significantly enhance production efficiency by performing complex multi-surface machining in a single setup, reducing errors from multiple clamping operations, and ensuring high precision and consistency. Therefore, CNC five-axis gantry machining centers hold an indispensable position in modern manufacturing.
Due to their powerful machining capabilities and flexibility, CNC five-axis gantry machining centers excel in processing complex geometric shapes, particularly in the production of high-precision molds and aerospace components. Additionally, their versatility allows them to accommodate a wide range of materials, including aluminum alloys, stainless steel, titanium alloys, and composite materials, further expanding their application scope.
The advanced control systems of CNC five-axis gantry machining centers precisely manage toolpath trajectories, ensuring extremely high machining precision and surface quality, which is crucial for producing high-performance parts that require meticulous surface finishing and tight tolerance ranges.
Features of CNC Five-Axis Gantry Machining Centers:
1. Five-Axis Machining Capability:
CNC five-axis gantry machining centers have five motion axes (X, Y, Z, A, B), enabling machining in multiple directions. This allows for the processing of complex shapes, greatly enhancing flexibility and precision.
2. Gantry Structure:
The gantry design provides stable support and high rigidity, allowing CNC five-axis gantry machining centers to maintain high precision while machining large workpieces. This structure also increases the machining space, improving efficiency.
3. High-Precision Spindle:
Equipped with a high-precision spindle, CNC five-axis gantry machining centers can perform high-speed cutting and high-precision machining, improving surface quality and dimensional accuracy.
4. High Rigidity and Stability:
The gantry structure provides excellent rigidity and stability, enabling the machine to withstand high machining forces, which improves overall machining accuracy.
Precision Technology:
1. Linear and Circular Error Compensation:
Advanced CNC systems and measurement instruments are used for linear and circular error compensation, enhancing machining accuracy in CNC five-axis gantry machining centers.
2. Dynamic Compensation Technology:
Through dynamic measurement and compensation technology, real-time error corrections are made during the CNC machining process, ensuring high-precision machining.
3 Thermal Deformation Compensation:
Compensation for thermal deformation is performed to maintain accuracy when the CNC five-axis gantry machining center operates for extended periods or in high-temperature environments.
4. Precision Feed System:
CNC five-axis gantry machining centers are equipped with high-precision feed systems (such as servo motors and high-precision ball screws), ensuring the accuracy of each machining step.
5. High-Precision Measurement System:
Equipped with advanced measurement systems (such as optical scales or laser measurement systems), CNC five-axis gantry machining centers monitor and adjust machining precision in real-time.
In conclusion, CNC five-axis gantry machining centers are indispensable high-end equipment in modern manufacturing. Whether in aerospace, high-end mold manufacturing, or energy equipment and automotive parts production, they play a key role in achieving high-quality product manufacturing due to their precision, multi-axis coordination, and exceptional stability.