
Technology
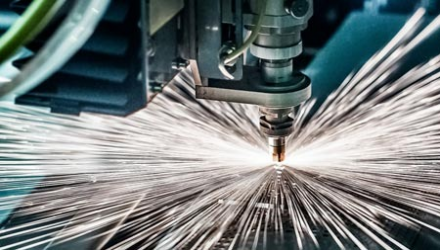
Principles and Types of Laser Cutting
Laser cutting is an advanced material processing technology that utilizes high-energy laser beams to cut materials with exceptional precision, efficiency, and flexibility. In modern manufacturing, laser cutting plays a crucial role due to its ability to deliver high-quality cuts on various materials. The core principle of laser cutting involves using the laser beam to locally heat the material to a molten or vaporized state, achieving precise cutting results. Laser cutting is effective not only for metals like steel, stainless steel, aluminum, and copper but also for non-metal materials such as plastics, wood, and glass. This makes it widely applicable across industries such as automotive manufacturing, aerospace, electronics, construction, and art.
Principle of Laser Cutting
The basic principle of laser cutting technology is to use a high-energy laser beam to locally heat the material, causing it to melt, vaporize, or burn at the focal point. The molten material is then blown away by air or other assistive methods, allowing for precise cutting. During the laser cutting process, the laser beam is focused into a high-energy spot by an optical system, which quickly and effectively cuts through materials like metals, plastics, and wood. Laser cutting features advantages such as non-contact processing, high precision, and minimal heat-affected zones, making it widely used in many high-end manufacturing fields.
Types of Laser Cutting
1. CO2 Laser Cutting
CO2 laser cutting is one of the earliest and most widely used laser cutting technologies. With a wavelength of 10.6 micrometers, CO2 lasers are primarily used for cutting and engraving non-metal materials like plastics, wood, and textiles. CO2 lasers offer high power and precision, making them suitable for processing thicker materials. Common industrial applications include automotive parts manufacturing, advertising signage production, and woodworking.
2. Fiber Laser Cutting
Fiber laser cutting technology uses fiber lasers to generate high-power laser beams with a wavelength of about 1.06 micrometers. Compared to CO2 lasers, fiber lasers have better beam quality and lower energy loss, making them ideal for cutting metals such as stainless steel, aluminum, and copper. Advantages include high speed, precision, and energy efficiency, with applications in electronics manufacturing, aerospace, and metal processing.
3. YAG Laser Cutting
YAG lasers (Yttrium Aluminum Garnet lasers) have a wavelength of 1.064 micrometers and are another common laser cutting technology. YAG laser cutting is suitable for cutting and welding metals, particularly under high-precision and high-strength requirements. This technology is frequently used in medical device manufacturing, metal parts processing, and high-tech industries.
4. Solid-State Laser Cutting
Solid-state laser cutting uses solid-state laser sources, such as YAG lasers or Nd lasers, to produce high-energy laser beams. This technology has high energy conversion efficiency and stable beam quality, making it suitable for cutting various metals with high precision. Solid-state lasers are widely used in automotive, aerospace, and precision instrument manufacturing.
5. Semiconductor Laser Cutting
Semiconductor laser cutting utilizes lasers produced by semiconductor sources, typically with wavelengths between 0.8 and 1.0 micrometers. This technology is suitable for fine cutting of thin metal and plastic materials, mainly used in electronics component manufacturing and micro-device processing.
Applications of Laser Cutting
Laser cutting technology is extensively used across various industries, including electronics manufacturing, automotive, aerospace, construction, and art production. Due to its high precision, low thermal impact, and non-contact processing capabilities, laser cutting plays a key role in many demanding manufacturing environments.