
Technology
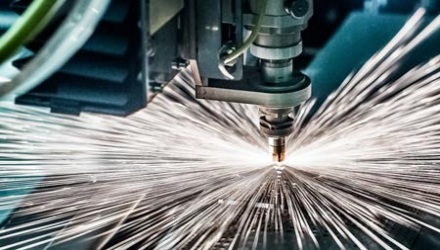
Industrial Applications of Laser Cutting
Laser cutting technology is a modern, high-precision material processing method that has become a core technology in today’s manufacturing industry due to its outstanding cutting performance and diverse application scenarios. The fundamental principle of laser cutting involves focusing a high-energy density laser beam precisely on the material's surface, achieving efficient cutting through melting, vaporizing, or ablating the material. The core advantages of this technology are its unmatched precision, efficiency, and flexibility. Here are specific applications of laser cutting in major industries:
1. Automotive Industry
In the automotive industry, laser cutting is widely used for producing body parts, interior components, and functional parts. It allows precise cutting of steel, aluminum, and other metals, meeting the high precision and complexity requirements of the automotive sector. Laser cutting enhances part quality, performance, and safety while reducing material waste.
2. Aerospace
Laser cutting plays a crucial role in the aerospace sector. It handles high-strength aerospace alloys and composite materials, enabling precise cutting of complex structural components. Laser cutting is used to manufacture aircraft structural parts, engine components, and other high-precision aerospace equipment. Its high precision and low heat-affected zone make it widely applicable in this field.
3. Electronics
In electronics manufacturing, laser cutting is employed to process various electronic components, enclosures, and brackets. It accurately cuts thin metal and plastic sheets to meet the fine processing requirements of electronic products. The technology's high precision and clean cutting characteristics help ensure the reliability and performance of electronic devices.
4. Construction and Decoration
Laser cutting is also significant in the construction and decoration industries. It is used to create complex decorative metal panels, engraved panels, and architectural elements. The flexibility of laser cutting meets innovative design needs in construction, allowing for unique and intricate design details while handling materials of various thicknesses.
5. Medical Equipment
In the medical equipment manufacturing field, laser cutting is used for producing high-precision medical instruments and components. It processes various biocompatible materials like stainless steel, titanium alloys, and medical-grade plastics, creating surgical tools, implants, and diagnostic devices. Its precision and low thermal impact ensure high performance and safety of medical equipment.
6. Signage
Laser cutting is extensively used in the signage industry to create various shapes and sizes of signs, letters, and decorations. It can precisely cut different materials such as acrylic sheets, metal plates, and wood, achieving creative designs and high-quality results. Laser cutting enhances the aesthetics and durability of signage, improving brand image and visibility.
7. Packaging Industry
In the packaging industry, laser cutting is employed to create precise packaging templates and molds. It processes various packaging materials, including cardboard, plastics, and films, achieving high-precision cutting and perforation to meet packaging design requirements. Laser cutting improves overall packaging quality and allows for quick design adjustments to accommodate different product needs.
8. Arts and Crafts
Laser cutting is increasingly used in the arts and crafts sector. Artists and craftsmen utilize laser cutting technology to create intricate artwork, engraved pieces, and crafts. The technology’s high precision and flexibility allow for complex design details and fine craftsmanship, catering to artistic creation and handmade production needs.
Laser cutting technology, with its exceptional precision, rapid production capabilities, and high efficiency, has become a key tool across industries. Its micrometer-level cutting precision and non-contact nature ensure minimal material damage and stable cutting edges. Additionally, the high material utilization and low waste emissions support environmental requirements, while smart control and full automation systems significantly enhance production efficiency, effectively addressing the fast-changing market demands.