
Technology
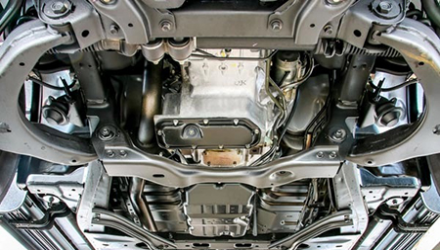
What is Sheet Metal Fabrication
Sheet metal fabrication is a specialized manufacturing process that involves cutting, bending, punching, stretching, welding, and forming metal sheets into desired shapes and structures. This process offers high flexibility and precision, handling a wide range of metals such as steel, stainless steel, aluminum, copper, and more, making it widely applicable across various industries.
In modern manufacturing, sheet metal fabrication plays a crucial role, especially in sectors like automotive, aerospace, home appliances, electronics, and construction. It efficiently transforms flat metal sheets into complex three-dimensional structures, such as car bodies, airplane wings, home appliance casings, electronic enclosures, and building frameworks.
The key advantage of this technique lies in its versatility, enabling full-process production from initial cutting to final assembly. It maintains high accuracy and consistency, allowing customized production of complex shapes. Whether for mass production or custom designs, sheet metal fabrication can meet design requirements at lower costs and with greater efficiency.
Additionally, sheet metal fabrication not only focuses on functionality and structural strength but also places strict requirements on the appearance and surface treatment of products. Through various surface finishing techniques such as polishing, painting, and electroplating, the final products possess excellent physical performance while showcasing aesthetic appeal, suitable for various applications.
With its exceptional processing capabilities and wide application prospects, sheet metal fabrication has become an indispensable part of modern industrial manufacturing. Its flexibility and precision ensure that this technology continues to hold a vital position in the face of ongoing innovation and development.
Key Processes
1. Shearing:
•Cutting metal sheets to size using shearing machines for straight cuts.
2. Punching:
•Creating holes or shapes in metal sheets using a punch press.
3. Bending:
•Forming metal sheets into specific angles or shapes using a press brake.
4. Deep Drawing:
•Stretching metal sheets into deep shapes like cups or shells.
5. Welding:
•Joining metal components through processes like MIG, TIG, or spot welding.
6. Forming:
•Pressing or extruding metal sheets into complex 3D structures using molds.
7. Surface Finishing:
•Polishing, painting, or plating to enhance appearance and durability.
8. Materials
•Common materials include steel, stainless steel, aluminum, copper, and brass, selected for their strength, workability, and durability.
Applications
1. Automotive:
• Car bodies and structural parts such as doors, roofs, and chassis.
2. Aerospace:
• Aircraft components like wings, fuselage skins, and structural supports.
3. Home Appliances:
• Metal housings for refrigerators, washing machines, and microwaves.
4. Construction:
• Roofing panels, wall panels, and ductwork for buildings.
5. Electronics:
• Enclosures for computers, servers, and electrical control boxes.
Advantages
1. Flexibility:
• Sheet metal fabrication can produce various shapes and sizes to meet different design needs.
2. Cost Efficiency:
• For mass production, this process offers lower unit costs.
3. Durability:
• Processed metal sheets have high strength and can withstand harsh conditions.
Sheet metal fabrication is a versatile, efficient, and widely applicable manufacturing technique, playing a vital role in industries ranging from everyday goods to high-tech equipment.