
Technology
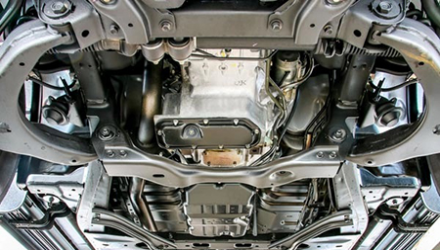
The main processes of sheet metal fabrication
Sheet metal fabrication is a multi-step manufacturing process widely used across various sectors of modern industry. The main process of sheet metal fabrication involves several stages, from design to the final product, with each step playing a crucial role in determining the quality and precision of the final product. Below is a detailed overview of the primary steps involved in sheet metal fabrication:
1. Design and Drawing
The first step in sheet metal fabrication is design and drawing, which forms the foundation of the entire process. Designers use CAD software to create 3D models and detailed drawings of the product. These designs dictate the steps and materials needed for fabrication, ensuring that the final product meets the required precision and functional standards.
2. Material Selection and Cutting
In sheet metal fabrication, selecting the right material is crucial. Based on design requirements, the appropriate metal, such as steel, stainless steel, or aluminum, is chosen. The process then moves to cutting, where technologies like laser cutting, water jet cutting, or shearing are used to accurately cut the material into the required shapes and sizes, preparing it for the next steps.
3. Stamping and Forming
Stamping and forming are key steps in sheet metal fabrication. Using dies and presses, the cut sheets are shaped into specific forms or features such as holes, grooves, or protrusions. This step is critical, as it determines the structural strength and final shape of the product.
4. Bending
Bending is a common process in sheet metal fabrication where a press brake is used to fold the sheet along specific lines to achieve the desired angles. The accuracy of bending directly affects the assembly and appearance of the final product, requiring high skill and precise control.
5. Welding and Assembly
Welding and assembly are essential stages of sheet metal fabrication that join multiple parts together to form a complete structure. Welding techniques such as fusion welding and TIG welding are widely used to ensure the strength and durability of the joints, enhancing the overall quality of the product.
6. Surface Treatment
Surface treatment is a critical step in sheet metal fabrication. Techniques like sandblasting, electroplating, anodizing, and powder coating are used to provide corrosion resistance and improve the aesthetic appeal of the products, further enhancing their durability and market competitiveness.
7. Quality Inspection and Testing
Quality inspection and testing are vital steps in sheet metal fabrication. Before the products are shipped, they undergo rigorous checks for dimensional accuracy, weld quality, and surface treatment results, ensuring that the products meet design specifications and expected performance standards.
8. Packaging and Shipping
In the final stage of the sheet metal fabrication process, the qualified products are appropriately packaged to prevent damage during transportation. Packaging and shipping are crucial steps to ensure the products reach the customers safely.
Through these key processes, sheet metal fabrication technology can transform metal sheets into workpieces of various shapes and functions, widely applied across industries. Each step requires precise operations and a high level of expertise to ensure the quality and consistency of the final product.