
Technology
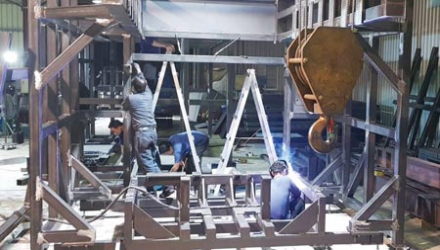
Welding Blowhole Issues
Welding blowholes typically occur when gases or impurities fail to escape during the welding process, leading to small holes or pores on the weld surface. These blowholes can compromise the quality and structural integrity of the weld. For welding frames, which require high strength and precision, blowhole issues are especially critical. Here are key measures to avoid welding blowholes in frame welding:
• Surface Preparation:
Prior to welding the frame, thoroughly clean the material surface to remove oxides, grease, and other contaminants. A clean surface ensures that gases are not trapped during welding.
• Welding Environment Control:
Control the gas flow and ensure the quality of shielding gases during welding, especially when using CO2 or TIG welding. Proper gas coverage in the welding zone prevents air from entering the molten pool.
• Welding Parameter Adjustment:
Correctly setting the welding current, voltage, and speed is vital for frame welding. Welding heavy materials for frames requires precise current control; too much current can destabilize the weld pool, increasing the likelihood of blowholes.
• Welding Process Selection:
Choose appropriate welding processes such as TIG or MIG welding, which offer effective shielding and help reduce the risk of blowholes.
• Frame Welding Design:
When designing welded frames, minimize narrow or enclosed areas where gases may accumulate, as these areas are more prone to blowhole formation.
In summary, addressing welding blowholes requires attention to all aspects of the welding process, from material preparation and parameter settings to process selection. For critical structures like welding frames, quality control is essential. By implementing these measures, not only can the quality of the welded frames be improved, but also their safety and durability in various applications.