
Technology
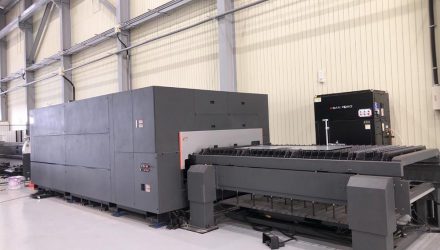
Key Techniques for Solving Burrs, Slag, and Inaccuracies in the Laser Cutting Process
The laser cutting process is a precise machining technique, but in practice, issues like burrs, slag, and uneven circular holes frequently occur. To solve these problems, the following techniques can effectively improve laser cutting quality:
• Cutting Parameter Adjustment
In laser cutting, adjusting the cutting speed and laser power is critical to reducing burrs and slag. If the laser cutting speed is too fast or too slow, it can result in incomplete cutting or rough edges. By accurately controlling laser power and cutting speed based on material properties, the laser cutting process can achieve smooth, burr-free edges.
• Optimization of Gas Parameters
Using the appropriate cutting gas is one of the core solutions to improving laser cutting quality. Nitrogen or oxygen is commonly used in the laser cutting process for different materials. The right gas pressure helps reduce slag and burrs, ensuring the surface quality of laser-cut workpieces.
• Material and Surface Preparation
Before starting the laser cutting process, the cleanliness of the material surface directly affects the cutting results. Removing oxide layers or oil residues from the material can significantly reduce burrs and slag, allowing for smoother laser cutting. Additionally, selecting materials with uniform thickness can enhance the precision of the laser cutting process, preventing issues like uneven circular holes.
• Cutting Path and Process Selection
Precise cutting path planning is crucial to the laser cutting process. Properly planning the cutting sequence and path can minimize material deformation. This is particularly important when performing laser cutting for circular holes or complex shapes. Optimizing the cutting path improves cutting accuracy, preventing irregular circular holes or rough edges.
• Equipment Maintenance and Technological Upgrades
Maintaining the performance of laser cutting equipment and ensuring the cleanliness of lenses and nozzles can significantly enhance the stability of the laser cutting process. Additionally, upgrading equipment control systems and servo motors can reduce burrs and slag during high-precision laser cutting, improving cutting efficiency.
Applications and Market Demand for Laser Cutting
With the increasing adoption of laser cutting technology, precision machining is becoming more prevalent across various industries. From automotive manufacturing to metal processing, the laser cutting process is the preferred machining technology due to its efficiency and precision. To meet the market's demand for high-quality workpieces, ongoing research and parameter optimization for laser cutting will continue to drive technological advancement.
In conclusion, by optimizing cutting parameters, gas selection, material preparation, and equipment maintenance, issues like burrs, slag, and uneven circular holes in laser cutting and laser cutting processes can be effectively resolved. These measures not only improve cutting quality but also enhance market competitiveness.