
Technology
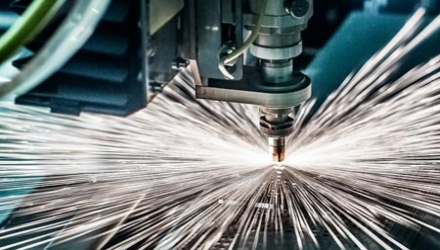
Optimize laser cutting and sheet metal processing time and cost.
Optimizing laser cutting and sheet metal processing time and cost significantly enhances production efficiency, reduces costs, and minimizes material waste. In a highly competitive market, streamlining processes and maximizing equipment usage accelerates delivery times, ensures product precision, and strengthens competitiveness to meet customer demands. Here are strategies to optimize laser cutting and sheet metal processing time and cost:
1. Enhance Laser Cutting and Sheet Metal Processing Equipment Efficiency
• Use High-Performance Fiber Laser Cutters: Fiber laser cutters, known for their high cutting speed and energy efficiency, are ideal for materials of varying thicknesses, significantly reducing processing time and saving energy. Wei Sheng Industrial utilizes equipment such as the MAZAK 3D FABRI GEAR MkIII 4.0KW tube laser cutter, KANFON laser cutter, and CNC hydraulic press brake to efficiently meet customer demands for precision components and metal products.
• Optimize Cutting Parameters: Adjust laser power, cutting speed, and gas flow according to material thickness and characteristics to ensure precise cutting and minimize material deformation.
2. Automate and Implement Smart Production
• Automated Loading and Unloading Systems: Automated systems reduce manual handling time, enabling 24/7 continuous production and enhancing efficiency.
• Intelligent Nesting Software: Automatic nesting software optimizes material layout and cutting paths, reducing scrap waste and increasing cutting speed.
3. Simplify Design
• Optimize Part Design: Reducing unnecessary small holes, sharp angles, and complex shapes in designs shortens cutting paths and lowers processing difficulty.
• Standardization and Modularization: For standard or high-volume products, standardized and modularized designs reduce setup and switching times.
4. Increase Material Utilization
• Accurate Nesting: Nesting software increases material utilization, minimizing waste and reducing costs.
• Scrap Recovery and Reuse: Consider recycling and reusing scraps to maximize material usage.
5. Regular Equipment Maintenance and Upkeep
• Routine Maintenance: Keep laser cutters and sheet metal processing equipment clean and calibrated to ensure stable operation, reducing failure risk and downtime.
• Extend Equipment Life: Regular maintenance lowers equipment failure rates, ensuring long-term stable operation.
6. Reduce Consumable and Energy Usage
• Use Appropriate Assist Gases: Selecting the right assist gases, such as nitrogen or oxygen, speeds up cutting, reduces oxidation, and lowers overall costs.
• Energy-Saving Mode and Auto Shutdown: Set machines to enter energy-saving modes or auto-shutdown during standby, reducing unnecessary energy consumption.
7. Employee Training and Skill Improvement
• Professional Skills Training: Training operators in equipment management and troubleshooting helps efficiently handle various materials and workpiece demands, reducing errors and improving precision.
• Workflow Optimization: Educating operators on the best cutting and nesting methods improves overall production efficiency.
8. Integrate Laser Cutting and Sheet Metal Processing Workflows
• Minimize Process Switching: Combine multiple steps into one workflow where possible to avoid frequent setup and switching, reducing production time.
• Efficient Production Scheduling: Arrange production sequences according to material characteristics and workpiece requirements to complete processing with the shortest path and fewest steps.
Located in Taoyuan, Taiwan, Wei Sheng Industrial is dedicated to providing professional metal processing services, including sheet metal processing, laser cutting, frame welding, CNC machining, CNC milling, gantry milling, and automated equipment assembly. Weisheng Industrial meets all customer requirements for precision components and metal products with high efficiency.