
Technology
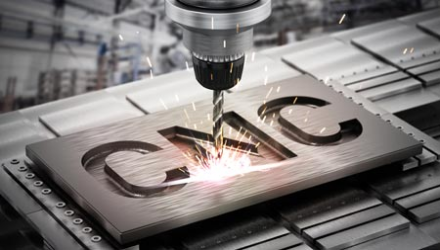
Common Defects and Solutions in CNC Machined Parts.
Common Defects and Solutions in CNC Machined Parts:
1. Dimensional Deviation
• Cause: Insufficient machine tool accuracy, tool wear, improper CNC machining parameters (such as cutting speed and feed rate).
• Solution: Regularly inspect and replace tools, ensure CNC machine calibration, and adjust appropriate machining parameters (such as cutting speed, feed rate, and depth).
2. Poor Surface Roughness
• Cause: Excessive cutting speed, improper tool selection, or incorrect CNC feed rate.
• Solution: Choose the appropriate tool material and cutting parameters, use suitable coolant to reduce friction and improve surface finish.
3. Burrs
• Cause: Improper cutting conditions, tool wear, or uneven material hardness.
• Solution: Optimize cutting parameters, select finer tools, and deburr after CNC machining.
4. Workpiece Deformation
• Cause: Excessive cutting force, improper fixation, or uneven coolant distribution.
• Solution: Reduce cutting depth or force, improve workpiece clamping, and use appropriate coolant to minimize temperature fluctuations.
5. Inaccurate Hole Diameter
• Cause: Incorrect tool selection, insufficient machine tool movement accuracy, or incorrect feed speed.
• Solution: Use specialized drilling tools, adjust feed rate, ensure machine tool precision, and select the correct machining parameters.
6. Chip Defects
• Cause: Inefficient chip removal, leading to heat buildup, affecting surface quality.
• Solution: Adjust CNC machining cutting parameters (such as feed rate and cutting depth), enhance the cooling system, and ensure smooth chip removal.
7. Vibration Defects
• Cause: Vibration from the tool, workpiece, or machine tool structure, causing surface ripples or fluctuations.
• Solution: Reduce feed speed, increase machine rigidity, optimize tool setup, and maintain stable CNC machining conditions.
8. Corner Chipping Defects
• Cause: Excessive cutting force or improper tool angles during machining, causing tool breakage.
• Solution: Select appropriate tool materials and geometries, control cutting forces, and avoid excessive cutting depth or feed rate.
9. Edge Burr Defects
• Cause: Excessive feed speed, unstable cutting forces, or inadequate cooling, causing burrs on CNC machined part edges.
• Solution: Optimize cutting parameters, use finer tools, and improve the cooling and lubrication system to reduce edge deformation.
10. Built-up Edge (BUE) Defects
• Cause: Ineffective chip removal, leading to chip adhesion on the tool and affecting the CNC cutting process.
• Solution: Adjust cutting parameters, choose the appropriate coolant to reduce chip buildup, and ensure smooth chip removal.
11. Cutting Marks or Tool Scratches
• Cause: Marks left by the tool during CNC machining, often due to incorrect tool installation, excessive or insufficient tool edge angle, or unsuitable tool material.
• Solution: Ensure correct tool installation, select appropriate tool materials, and adjust tool geometry and CNC machining parameters based on workpiece material.
12. Material Cracking or Damage
• Cause: Material cracks or damage during CNC machining, often caused by excessive cutting forces or improper tool settings.
• Solution: Reduce cutting forces, select appropriate tools and cutting parameters, and use suitable coolant to reduce stress during CNC machining.
These defects can be resolved by adjusting CNC machining parameters, selecting suitable tools, enhancing equipment maintenance, and improving machining conditions to increase CNC machining accuracy and efficiency.